
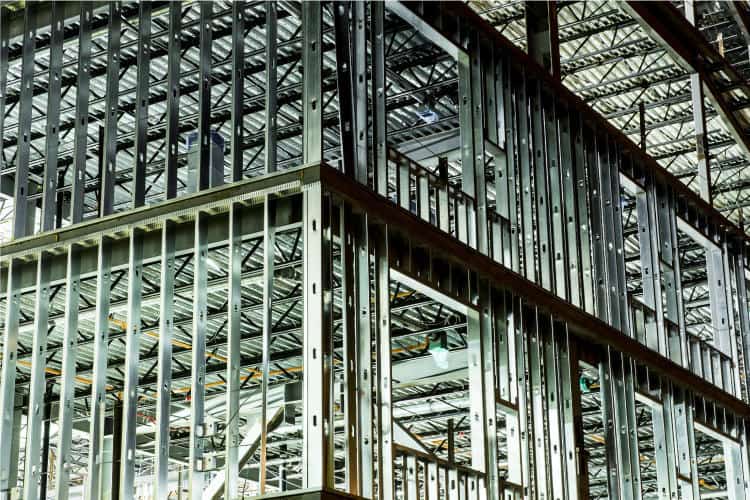
Composite action is a result of T-beam-like action between the repetitive member and connected sheathing, but is limited by nail slippage in the connection. Additionally, the connected sheathing increases the bending capacity of bending members due to both composite action and load sharing. The behavior of the individual members, then, is affected by inclusion into this system. These members must also be joined by a load distributing element adequate to support the design load. A repetitive system is one of at least three members that are spaced not farther apart than 24-inches. Typical light-frame wood construction consists of floor, roof, and wall systems, each with repetitive members connected by sheathing. Currently, however, the bending strength of cold-formed steel repetitive members is not permitted to be increased, even though the method of framing is quite similar to that of wood except for the material properties. For wood framed structures with repetitive members, a repetitive member factor increases the allowable bending stress from 1.00 to 1.50 times the reference design value, depending on both the type of material and the type of load.
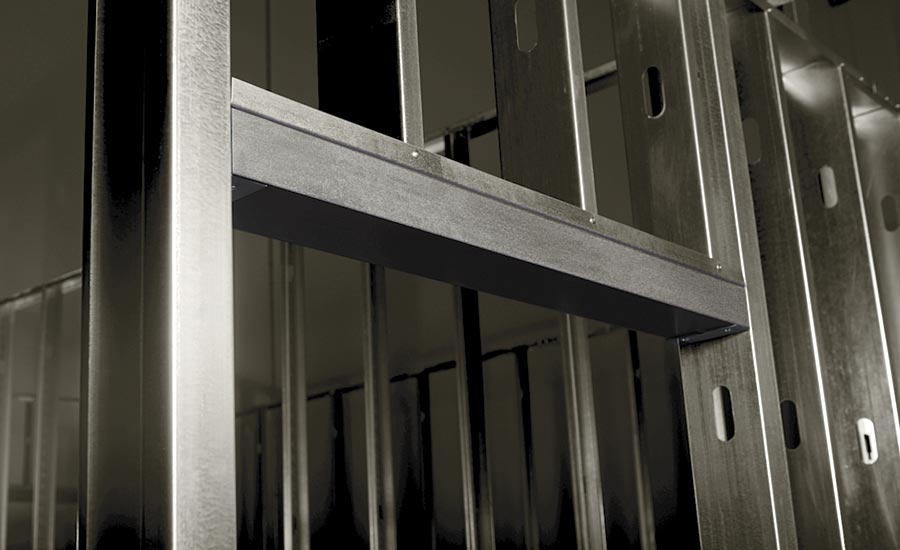
formed steel has become a preferred building material for structural farming in many different types of structures, commonly for repetitive members such as floor joists, roof rafters, roof trusses and wall studs. Contact us for a quote on your next office building, high rise or apartment complex. It’s a simple yet effective process for creating high-quality framing components.Īs a commercial installer, UBS is a leader in metal stud framing. The CFS components are made by pressing and rolling steel at room temperature. To recap, CFS framing involves the use of cold-formed steel studs, joists and other components. The good news, however, is that framing studs, joists and other components are available in CFS. Since its made of inorganic material, it won’t succumb to moisture damage, nor will wood-boring pests feast on it.īecause of their room temperature manufacturing process, CFS products are limited to just a few basic shapes. Like all steel products, CFS isn’t susceptible to rot, mold or termites. Furthermore, the standardized specifications of CFS promotes faster installation, allowing construction companies to finish their projects more quickly. It’s easier to manufacture than hot-formed steel, resulting in a lower price. They are stronger than hot-formed steel products, making them a particularly attractive choice for commercial framing.ĬFS framing is also cost effective for construction companies. According to the American Iron and Steel Institute, CFS steel products have an average yield strength of 33 to 50 kilopounds per square inch (ksi). There are several benefits to using CFS studs to frame a building, one of which is increased strength. The high temperatures to which hot-formed steel is exposed causes structural changes, making it difficult to manipulate. This makes the steel easier to manipulate and bend but at the cost of strength. With hot-formed steel, the steel materials are heated to temperatures of 1,700 degrees Fahrenheit or higher. The key difference between CFS and hot-formed steel is that the former involves a room temperature production process, whereas the latter involves a heated production process. Cold-Formed vs Hot-Formed Steel: What’s the Difference? These CFS products are then installed to create the frame of a building. CFS studs are made using a special process in which steel materials are rolled – at or near room temperature – into various shapes to create steel products such as studs and joists. Just because two studs are made of steel doesn’t necessarily mean that they feature the same type of steel. What Is Cold-Formed Steel FramingĬold-formed steel framing refers to the use of CFS studs to frame a building. There are different types of steel, however, one of the most popular of which is cold-formed steel (CFS). Steel is strong, resistant to moisture and lasts a long time, making it ideal for framing. Steel studs are often preferred over wood because of the increased strength and durability offered by this iron alloy.
